矩阵软件自动装车技术是一种基于先进的传感器、机器视觉、人工智能等技术,实现货物快速、准确、高效装车的解决方案。它在物流行业中起着至关重要的作用,能够极大地提高物流效率。例如,在煤炭行业,自动装车技术不仅可以提高生产效率和产能,还能减少工人劳动强度,降低运输成本。据统计,采用自动装车技术后,煤炭企业的装车效率可提高 30% 以上,同时降低人工成本约 40%。在制造行业,智能自动装车系统可以实现 24 小时不间断自动装车,大大提高了装车效率和准确性,降低了人力成本。此外,自动装车技术还能提高货物安全性,通过精确计量和定位,避免货物损坏或丢失,确保货物的安全性和稳定性。
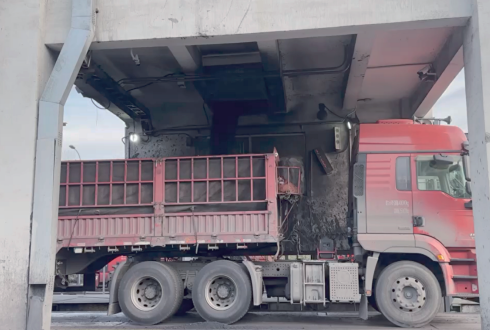
(二)自动装车技术的发展历程
自动装车技术的发展历程可以追溯到上个世纪 90 年代初,当时采用的是雷达、激光等传感技术实现砂石装载的自动化。然而,由于当时技术不够成熟,这些系统的应用受到了很多限制,并未得到广泛的推广应用。随着计算机技术、人工智能技术、传感技术等的持续发展,自动装车技术也变得更加成熟。目前,市场上已经有较为成熟的产品,如 Volvo 的自动化装载系统、Caterpillar 的自动化砂石装载系统等。这些系统采用了高精度的位置和质量传感器以及先进的控制算法,实现了砂石的自动装载、称重、运输等一系列自动化操作。在煤炭行业,自动装车技术也在不断发展。从传统的人工装车到现在的无人自装,防漏防溢的智能化装车系统,煤炭企业的装车效率和安全性得到了极大的提高。同时,在其他行业,如面粉、玉米粮食颗粒物料等领域,全自动装车设备也得到了广泛的应用。
二、自动装车技术的优势
(一)提高作业效率
自动装车技术采用先进的自动化设备和控制系统,能够快速完成装车任务。例如,在煤炭行业,自动装车系统可以实现连续快速地进行装车作业,不受人工疲劳和工作时间限制,可实现 24 小时不间断作业,大大增加了产能输出。以某大型煤矿为例,采用自动装车技术后,原本数小时才能完成的一列火车装车任务,现在仅需一两个小时,装车效率提高了 50% 以上。在其他行业,如化工颜料、染料行业,无人装车系统采用先进的自动化技术,可以实现快速、准确地装车,大幅提高装车效率,减少人工操作的时间和成本。
(二)保证装载精度
自动装车技术通过高精度的传感器和智能控制系统,能够精确控制装载量,使货物分布均匀,提高运输安全性。例如,在火车煤炭自动装车技术中,通过对车厢位置、煤炭流量和重量的实时监测,由控制系统精确计算和控制煤炭的装载量和分布,以确保每节车厢都能准确、均匀地装满煤炭。装载精度误差可控制在 1% 以内,使煤炭在车厢内分布更均匀,避免重心偏移,提高运输安全性。在冰晶石、铁粉全自动装车系统中,配备高精度的称重传感器和测量装置,确保了装车货物的准确性和平衡性,避免了人工装车时出现的数量误差和安全事故。
(三)降低劳动强度与成本
自动装车技术减少了人工参与,降低了劳动强度和工伤风险,同时节省了人力成本。在传统的装车方式中,需要大量的人力进行搬运和操作,劳动强度大,工作环境恶劣,容易导致工人疲劳和受伤。而自动装车技术可以完全替代人工进行装车作业,节省了大量的人工成本。以湖南省湘衡盐化有限责任公司的自动装车设备为例,通过设置双向运输组件可以将盐袋进行自动运输装车处理,不需要人工进行搬运,大大减低了人工成本。在煤炭行业,自动装车技术减少了人工参与装车的繁重体力劳动,工人无需在恶劣的环境中长时间作业,降低了因高强度劳动导致的工人疲劳和潜在的工伤风险。
(四)提升安全性
自动装车技术降低了工人在装车现场的暴露风险,减少了事故发生的可能性。在传统的装车方式中,工人需要在高处或危险区域作业,容易发生安全事故。而自动装车技术可以避免人工在高处或危险区域作业,降低了事故发生的可能性。例如,在氮肥厂应用全自动装车机器人设备,可以减少人工接触危险化学品的机会,降低了工人在搬运过程中发生安全事故的风险。同时,全自动装车机器人设备还可以避免因超载等原因造成的安全隐患。
(五)优化资源利用与环保效果
自动装车技术精确装载控制减少了浪费,提高了资源利用率,降低了环境污染。自动装车技术能够精确控制每节车厢的装载量,减少超载或欠载的情况发生,提高了煤炭资源的利用率。同时,精准控制减少了煤炭在装车过程中的扬尘和撒落,降低了对环境的污染。例如,某大型煤矿在采用火车煤炭自动装车技术后,因减少煤炭撒落和扬尘,周边环境质量得到明显改善。在砂石行业,自动装车技术的应用可以减少装载过程中的人为误差,提高工作质量,同时减少了煤尘的飞扬和装载时的物料损耗,进而降低了环境污染和成本支出。
四、自动装车技术的发展趋势
(一)人工智能与大数据应用
随着科技的不断进步,人工智能与大数据在自动装车技术中的应用越来越广泛。自动装车系统可以通过收集大量的装车数据,利用大数据分析技术,对不同货物类型、车辆尺寸、装载环境等因素进行分析,从而实现智能路径规划。例如,根据货物的重量、体积和形状,以及车辆的承载能力和空间布局,自动规划出最优的装载方案,提高空间利用率和装载效率。同时,结合人工智能算法,自动装车系统可以实现动态调度。当出现突发情况,如车辆故障、货物变更等,系统能够迅速调整装车计划,重新规划路径,确保装车作业的顺利进行。据统计,采用人工智能与大数据技术的自动装车系统,其装载效率可提高 20% 以上,空间利用率提高 15% 左右。
(二)无人化与智能化趋势
无人化与智能化是自动装车技术未来的重要发展方向。为了实现无人化,自动装车技术需要研发更先进的导航定位技术。例如,利用高精度的激光雷达、视觉传感器和全球定位系统,实现对车辆和货物的精准定位。同时,结合智能控制算法,自动装车系统可以自主完成装车作业,无需人工干预。在智能化方面,自动装车系统可以通过学习和优化算法,不断提高自身的性能和适应性。例如,根据不同的装车场景和需求,自动调整装载策略,实现更加高效、精准的装车作业。目前,一些先进的自动装车系统已经实现了高度的无人化和智能化,未来这一趋势将更加明显。
(三)服务能力提升
自动装车企业不仅要提供先进的技术产品,还需要提升服务能力,为客户提供定制化解决方案和优质的售后服务。对于不同行业的客户,其装车需求和场景各不相同,自动装车企业需要根据客户的具体情况,提供定制化的解决方案。例如,对于化工行业,需要考虑危险化学品的特殊装载要求;对于食品行业,要确保装载过程的卫生和安全。同时,加强售后服务也是提升服务能力的重要方面。自动装车系统在运行过程中可能会出现各种问题,企业需要及时响应客户的需求,提供快速、专业的维修和技术支持。据调查,提供优质售后服务的自动装车企业,其客户满意度可提高 30% 以上,市场竞争力也会显著增强。
五、自动装车技术的案例分析
(一)煤炭行业案例
在煤炭行业中,自动装车技术的应用带来了诸多显著成效。例如山西某大型煤矿采用先进的火车煤炭自动装车系统后,通过高精度的传感器和智能控制系统,实现了对煤炭流量和车厢位置的精确把控。系统能根据不同类型的车厢自动调整装车策略,确保煤炭均匀分布且装载量达到最佳。以往人工装车一列火车需要 6 小时左右,现在自动装车仅需 3 小时,而且装载精度误差控制在 0.5% 以内。
内蒙古某煤炭运输枢纽引入自动化装车技术后,有效解决了过去因人工操作导致的装载不均匀和超载问题。系统实时监测车厢的载重情况,并自动控制给料量。同时,通过优化装车流程,减少了煤炭的撒漏和扬尘,不仅提高了运输效率,还降低了环境污染。据统计,每年因减少煤炭撒漏节省的成本达到数百万元。
河北某煤炭企业在应用自动装车系统之前,经常面临因装车不精准而导致的运输纠纷。自从采用自动装车系统,每节车厢的装载量都能严格按照标准执行,提高了客户满意度。此外,由于装车过程的自动化,减少了人工干预,降低了安全事故的发生率。
新疆某煤矿地处偏远地区,劳动力相对短缺。引入火车煤炭自动装车技术后,大大缓解了人力不足的问题。系统能够在恶劣的环境条件下稳定运行,实现 24 小时不间断装车作业。不仅提高了煤炭的外运量,还为企业在市场竞争中赢得了优势。
(二)水泥行业案例
北元集团水泥有限公司数字化自动袋装水泥装车线正式投运,率先在榆林区域实现袋装水泥全自动化装车,实现了从自动包装、转运、码垛的全智能一体化运作。司机只需将车停入装车区,通过扫码识别装车货物信息、数量,确认无误后,系统则通过 3D 激光雷达识别车型、车辆位置、车长以及其他尺寸结构的特征,借助内置的码垛算法和激光引导模块,系统能够自动识别并提供最佳的码垛方案。
数字化自动袋装水泥装车线投运后,不仅减少了大量搬运工作,同时也避免了装车过程中的扬尘以及水泥损耗,更减少了高温、粉尘对员工的危害;数字化、智能化控制大大提高了装车效率以及空间利用率,从原本人工装车每小时 50 吨提高至 80 吨,装车效率提升 60%。一线员工也实现了岗位的 “升级”,由繁重的体力劳动者转变为设备监督与管理者,工作环境更舒适,也减轻了工作负担。员工作业风险也大大降低。
中建材凯盛机器人针对国内水泥企业特点开发水泥智能装车机器人,在洛阳中联实施的全封闭式机器人装车系统,自动适应当前所有车型,在提升发运效率的同时,彻底解决了水泥发运环节粉尘无组织排放问题。同时,由于实现了全程污染管控,也有效保障了员工身体健康,避免了职业病危害。
新合海机械取得袋装水泥自动装车除尘系统专利,通过安装架上的吸尘机,在连接管和吸尘口的配合下,能够将产生的水泥粉尘抽入,经过吸尘机送至收集箱内进行收集,实现除尘的作用,可有效的避免水泥粉尘对工作人员造成伤害。
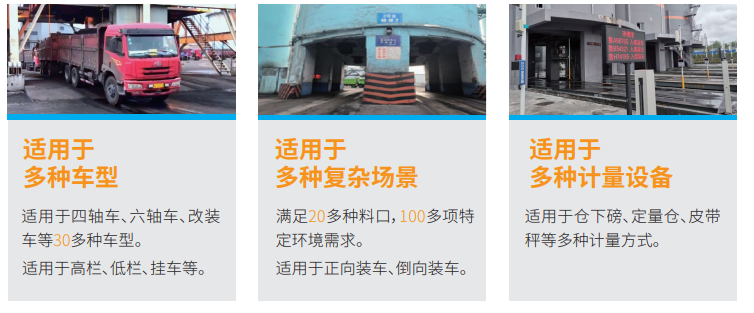
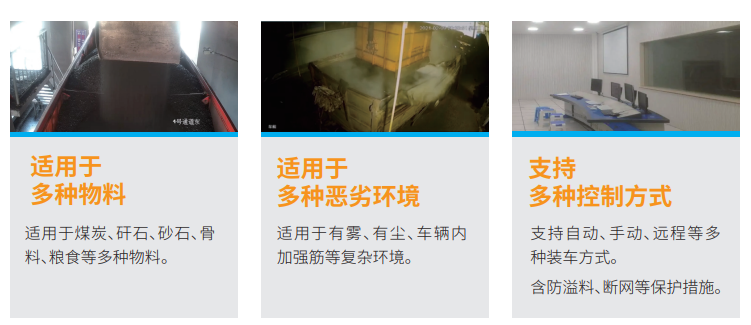
六、自动装车技术的挑战与未来展望
(一)自动装车技术面临的挑战
技术挑战
成本挑战
(二)自动装车技术的未来展望
技术创新推动发展
多方合作共同推动
市场前景广阔
总之,自动装车技术虽然面临一些挑战,但随着技术的不断创新和各方的共同努力,其未来发展前景广阔。自动装车技术将为物流行业带来更高的效率、更低的成本和更好的服务,推动物流行业向智能化、自动化方向发展。
矩阵软件在业界创新使用激光雷达三维点云建模分析技术及人工智能技术对装车过程进行控制, 利用
自研的AI智能检测算法 (Matrix-LoadDetector) 可对激光雷达点云动态数据进行实时分析,根据数学模
型实时计算料位高度与车厢高度的关系,综合判断最佳控制策略,实现无人值守高度智能化装车。可依据企业现有装车系统进行快速升级改造与上线,该系统已有400余条装车通道落地应用案例。